what you need to do small wire soldering
What is soldering?
Soldering is the joining of ii metal surfaces mechanically and electrically, with the use of metallic called solder. Solder secures the connection so it doesn't interruption loose due to vibration or other mechanical forces. It also provides electrical continuity, and then that the electronic indicate can travel through the connection without intermission. The solder is melted using a soldering iron. Flux is used to make clean and prep the surfaces, which allows the melted solder to flow (or "wet") and bail with the metal surfaces.
Hand soldering is the process of soldering 1 connection (called "solder joint") at a time, as opposed to more than automated soldering processes such every bit wave soldering (for thru-hole components) or reflow soldering (for SMT components).
What do I need to solder electronics?
When soldering an electronic connector to a contact point (oftentimes called a "pad"), you generally need the following:
- A soldering iron capable of reaching the melting point of the solder.
- Wire solder, with or without a flux core.
- Flux, if the wire solder does not include a flux core or if additional flux is needed.
What is a soldering atomic number 26?
A soldering atomic number 26 is a hand tool used to solder 2 metallic surfaces together. At its simplest form, information technology consists of a metallic tip, a heating element that brings the tip up to soldering temperature, an insulated handle to allow rubber belongings of the soldering iron, and a plug for either a wall outlet or the soldering station.
The soldering tip'south chore is to transfer heat from the heating element to the work. It has a copper interior, which acts as an constructive and efficient thermal conductor. It likewise has fe plating to protect the soft, corrosive-prone copper from flux and solder, and chrome-nickel plating to continue the flux from wetting up the tip.
Across that, there are options that provide ameliorate control over the soldering fe temperature and heat response (fourth dimension it takes to estrus up once again after soldering). These include soldering tips, which are metal slugs that rest against the heating element, and others which are integrated with the heating element in a cartridge.
What is the difference between a soldering atomic number 26 and a soldering station?
On the low cease, most appropriate for hobbyists, a soldering atomic number 26 may plug directly into the electrical wall outlet, which provides no control over soldering fe temperature. Only on or off. With a soldering station, the soldering iron plugs into the station for greater control over temperature, and other features like ready-temperature memory, lock-out, etc.
What type of solder should I use?
While there is a large variety of unlike types of solder, at the virtually basic, you need to choose between lead or lead-gratuitous, the diameter of the wire, flux cadre or solid wire, and the type of flux.
- Lead or atomic number 82-free – Solder is generally a combination of metals, which are chosen for the best reliability and conductivity. Pb, frequently combined with can, has been the mainstay of electronic soldering since its inception. Lead has a relatively low melting point and readily wets and flows, which makes the procedure faster, easier, and more fool-proof. Because of environmental and health concerns around, in that location has been pressure to move to lead-gratuitous solder, which is frequently a combination of tin and silver. Lead-free solders accept a higher melting point and generally require more active or more than full-bodied fluxes (higher solids content) to achieve the same soldering operation equally leaded solders. For typical transmission soldering, if done properly, reliability betwixt lead and lead-complimentary solders should exist most the same. For high-end electronics used in extreme environments (due east.one thousand. aerospace electronics), there are concerns with the tendency of bright can in pb-free solder to crystallize and form tin can whiskers -- sparse wires of tin that can grow from the solder joints.
If you lot are repairing or assembling electronics for use in the US, lead solder is the easiest to work with and it forms the most reliable solder joints. The lower heat also generates less thermal stress on the rest of the PCB. If the end product is being shipped outside of the United states, peculiarly to Europe, you should consider lead-free solder. An exception might exist for loftier-reliability electronics like those used in aerospace. In that case, check with the specifications and requirements of the end-user of the electronics. Lead-free may still be required, just at that place may be exemptions in place that permit for the use of lead solder.
- Diameter of solder wire – Make sure yous don't confuse solder wire intended for plumbing with solder wire intended for electronics. Wire for plumbing volition be much thicker, 2mm in bore or higher. Electronics solder wire will exist thinner, from i.5mm down to i/2mm, or even less. Lucifer the diameter to the size of the connectors and contacts y'all are soldering. If the bore of the wire solder is likewise small-scale, you will be going through as well much solder.Too large and it could be hard to maneuver around a dense PCB, thus increasing the chance of thermally stressing or even soldering other components that are unrelated to your repair.
- Flux core or solid wire – Virtually wire solder comes with a flux cadre, so the flux will automatically actuate and flow over the soldering surface area when the solder is melted. It is more convenient and efficient to work with. Solid wire tin can be used, with flux added past a brush, a bottle dispenser, or a pen dispenser. Unless a very specific flux is required that is non available as a wire solder core, flux core wire solder is generally recommended.
- Type of flux -- No-clean flux is a good choice for soldering where cleaning is to be avoided. The light rest can be left on the board, or removed with a flux remover. Rosin activated flux (RA) provides excellent solderability in a wide variety of applications. It is best to remove the balance afterward soldering for aesthetics and to avert corrosion downwards-the-line. Rosin flux (R) or mildly activated rosin flux (RMA) tin can generally exist left on the PCB after soldering unless aesthetics are a problem. H2o soluble flux (OA) is a very active flux engineered to be removed easily with DI water, like in a batch or in-line system. It can also be removed with isopropyl alcohol (IPA). It is very important to clean off h2o soluble flux residues because they are highly corrosive.
You may besides run into options for "element of group vii-costless" or "zero element of group vii". These classifications are for companies that have light-green initiatives, or have to comply with halogen restrictions due to regulatory or customer restrictions. Halogens include chlorine, fluorine, iodine, bromine and astatine elements. These can come with merchandise-offs like cleanability, so if y'all aren't required to eliminate halogens from your procedure, information technology is easier to stay with standard fluxes that incorporate halogens.
Should I utilise pb or lead-gratuitous solder?
If you are repairing or assembling electronics for utilize in the Usa, lead solder is the easiest to work with and it forms the most reliable solder joints. The lower heat as well generates less thermal stress on the rest of the PCB. If the end product is existence shipped exterior of the Us, especially to Europe, you should consider lead-free solder. An exception might be for loftier-reliability electronics similar those used in aerospace. In that case, check with the specifications and requirements of the finish-user of the electronics. Lead-costless may nevertheless be required, simply there may be exemptions in place that allow for the apply of lead solder.
What is flux?
Recollect of flux and a prepping agent for the soldering procedure. When joining two metal surfaces together with solder, there needs to be a good metallurgic bond, so that the solder joint doesn't break loose and electrical continuity doesn't fluctuate with mechanical, temperature, and other stresses. Flux removes whatever oxidation that may exist present and slightly etches the surface to promote wetting. "Wetting" is the process of solder flowing over the surfaces of the contacts and the soldering tip, which is very important in the soldering process.
What type of flux should I use?
No-make clean flux is a good choice for soldering where cleaning is to be avoided. The lite residual can exist left on the board, or removed with a flux remover. Rosin activated flux (RA) provides excellent solderability in a wide variety of applications. It is all-time to remove the residue afterwards soldering for aesthetics and to avoid corrosion down-the-line. Rosin flux (R) or mildly activated rosin flux (RMA) can generally be left on the PCB subsequently soldering unless aesthetics are a problem. Water soluble flux (OA) is a very active flux engineered to exist removed easily with DI h2o, like in a batch or in-line system. It tin also be removed with isopropyl alcohol (IPA). Information technology is very important to clean off water soluble flux residues because they are highly corrosive.
You may also run into options for "halogen-costless" or "zero halogens". These classifications are for companies that take green initiatives, or take to comply with element of group vii restrictions due to regulatory or customer restrictions. Halogens include chlorine, fluorine, iodine, bromine and astatine elements. These tin can come with trade-offs like cleanability, so if you aren't required to eliminate halogens from your procedure, information technology is easier to stay with standard fluxes that contain halogens.
Do I need to add together extra flux when soldering?
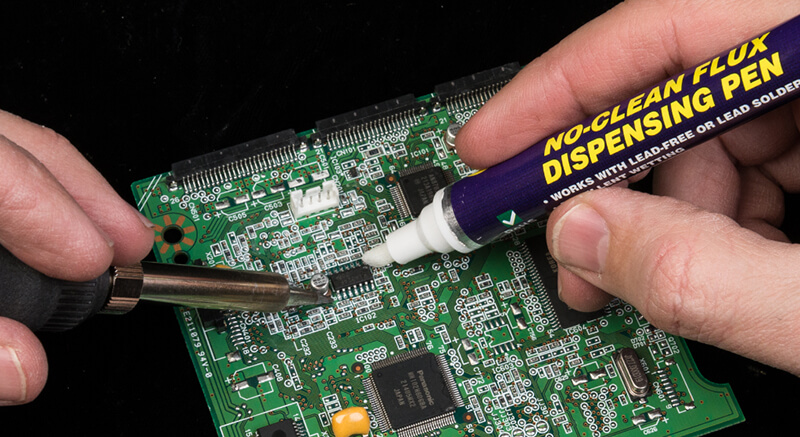
If soldering a simple connexion, similar ii wires, or a thru-hole atomic number 82, the flux in a flux core solder should be plenty. For more than complex soldering techniques, like drag soldering multiple leads on a surface mountain component, additional flux may demand to be added. The flux is activated and consumed when it originally flows from the core. If the solder is worked farther, like when you drag across multiple leads, you run the risk of cold joints or bridging without additional flux. While more flux seems like it should be better, take care not to over apply flux. Excess flux needs to be removed, especially if it isn't fully activated past being heated to total soldering temperature.
Associated products:
- Techspray No-Clean Flux Pen
- Plato Needle Dispensing Bottles
How do I employ extra flux?
Flux can be painted on with an acid castor, or practical with either a needle canteen dispenser, or a pen dispenser. While more flux seems like it should be better, have care not to over use flux. Excess flux needs to be removed, especially if it isn't fully activated by being heated to full soldering temperature.
Associated products:
- Techspray No-Clean Flux Pen
- Plato Needle Dispensing Bottles
- Techspray Technical Brush
How do I solder?
- Make sure the surfaces to exist soldered are clean.
- Plough on the soldering iron and set temperature above the melting signal of your solder. 600°- 650°F (316°- 343°C) is a good place to start for lead-based solder and 650°- 700°F (343°- 371°C) for lead-free solder.
- Agree the tip against both the lead and contact signal/pad for a few seconds. The idea is to bring both up to a soldering temperature at the same fourth dimension.
- Bear upon the solder wire to the lead and contact point/pad a few times until solder flows around the lead and contact.
- Inspect the solder joint to make certain in that location is total coverage over the contact area and the lead. If it is a thru-hole lead, the hole should be filled and the solder joint forms a slight pyramid-like shape.
- If necessary, trim the lead with a shear lead cutter. Do not trim into the solder joint, which can harm the connection.
- If using rosin activated flux, aqueous flux, or if the aesthetics of the flux residual is a problem, clean the area with a flux remover.
Associated products:
- Plato soldering tips
- Plato shear lead cutters
- Techspray G3 Flux Remover
- Techspray E-LINE Flux Remover
How hot exercise I set the solder iron?
600°- 650°F (316°- 343°C) is a skilful identify to kickoff for lead-based solder and 650°- 700°F (343°- 371°C) for pb-costless solder. You want the tip hot enough to cook the solder efficiency, but excess heat can damage components equally the heat travels along the leads, and it will reduce the lifespan of the soldering tip.
How do I tell a good solder joint from a bad one?
Inspect the solder joint to make sure there is full coverage over the contact area and pb. Some things to watch out for:
- If information technology is a thru-pigsty lead, the hole should exist filled and the solder joint forms a slight pyramid-like shape.
- If it is a surface mountain's solder articulation, the solder should fully cover the contact pad and surround the lead.
- The atomic number 82 should non be loose or jerk one time it is soldered.
- The solder shouldn't overflow or span onto other contact points/pads.
- If using lead-based solder, the solder joint should be shiny. Unfortunately, lead-free tends to accept a duller stop, and so shininess is not a good indicator in that example.
How do I select the best soldering tip for my PCB repair job?
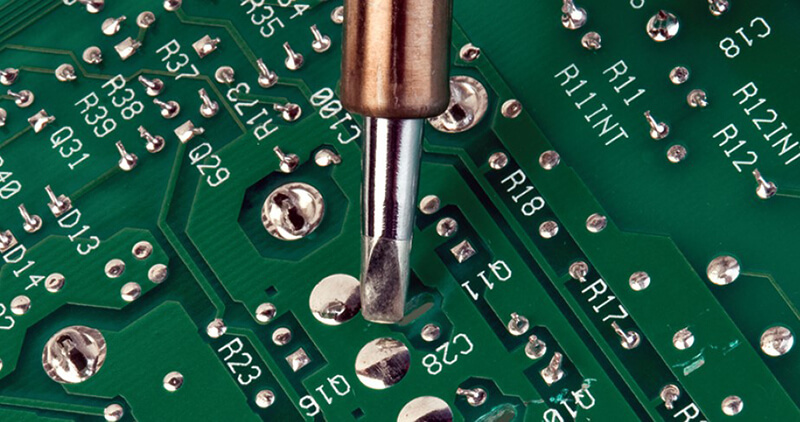
The goal is to lucifer the tip shape and size to the contact pad. This allows y'all to maximize the contact surface expanse, so that you lot oestrus the lead and contact area every bit quickly equally possible. If you lot choose a tip that is too big, you have more than tip volume to heat, which will dull down the estrus recovery - the time information technology takes for the tip to reheat subsequently soldering a joint. It as well runs the risk of interfering with other components and contact areas. If yous cull a tip that is too small, yous won't have enough surface area of the tip in contact with either the pb or the contact expanse to transfer heat efficiently. It will have more than dwell time, which slows you downwardly and could increment the thermal stress of the component.
Brand sure you are using a soldering iron and tips intended for electronic PCB soldering. Tips intended for other applications, like stained drinking glass, plumbing, or heavy electrical piece of work, are generally much larger than what is appropriate for electronics.
Soldering tips come in all kinds of shapes to facilitate different PCB geometries:
- Pointed or conical – The end of the soldering tip comes to either a point or a round the flat area. The size is specified past the diameter of the end, then it can range in size from 0.1mm to 1mm, or larger. These tips are by and large used when pivot-point accurateness is needed, like with very fine leadless surface mount components. They may be long for greater reach in dense board design, or take a shorter microtip to reduce the amount of tip metal that needs to be heated. This tin improve heat recovery. The ends of the tips may also be bent to avoid interfering with other components or contact areas.
- Blade or pocketknife – A blade tip is normally used for elevate soldering when the solder is fatigued across multiple contact pads. This is common when soldering surface mount applied science (SMT) components. The size is measured along the length of the blade and tin exist six.3mm (one/four") or larger.
- Chisel or screwdriver – A chisel allows you lot to heat a larger contact expanse, so information technology is useful for thru-hole solder joints. Lengths may vary and can also exist aptitude, similar with a conical tip. The size is mainly specified as the length of the apartment area, but the depth or thickness of the tip may besides vary. These can be and so small that they almost wait similar a point, similar under 1mm, and equally wide as v or 6mm.
- Bevel – A beveled tip has a flat oval terminate set at an bending. Picture show a metallic rod that is a cantankerous section at an bending. The size is specified by the bore of the "rod" or shaft and sometimes the bending of the bevel. A bevel can range from 1mm to 4mm, or even larger.
- Flow tips – A flow tip looks similar in design to a askew tip, but instead of a flat surface area, it is a little indention or loving cup. This is too called a "mini-wave tip", and is commonly used for drag soldering, every bit explained higher up.
Associated products:
- Plato soldering tips
Is it ok to fix the heat at maximum temperature to speed up soldering?
In soldering, similar everything else, speed is king. Operators volition turn up the soldering temperature to speed up heat throughput. This allows them to go from ane solder joint to the next faster. The catch – the higher the rut, the shorter the tip life. Sure, solder stations may go up to 900°F, simply 750°F is the highest you demand to go for a atomic number 82-free wire. The extra heat tin likewise unnecessarily stress components, increasing the chances of PCB failure later.
Why is the solder dripping off the soldering tip?
That is an indication that the soldering tip needs to exist cleaned, so it is a "cold" tip (although it is still very hot, so don't touch!). When flux and oxidation build up over time, the estrus does not transfer as effectively and the solder doesn't wet, or flow over the tip properly. The solder will tend to melt but but drip off the tip. This makes it difficult to movement in order to solder around contact areas the way you lot may need it.
How to clean a soldering iron?
Solder stations normally come with a sponge and/or brass "brillo" pad. The purpose is to remove excess flux and solder from the tip. If too much flux builds upwardly and burns onto the soldering tip, information technology will somewhen dewet and exist unusable (but non necessarily unrecoverable). Unless the tip cleaning tools are used properly, they tin can practise more damage than adept. When choosing a sponge, make sure it is made of natural cellulose (similar Plato replacement sponges). Synthetic sponges volition melt onto the soldering tip and can shorten tip life. Use clean DI water. Tap h2o may include minerals that tin build-up on the tip. When yous saturate the sponge, wring it out so that it is not dripping wet. Too much h2o tin increase the thermal stress of the tip, and slow downwards tip recovery.
When the soldering tip has turned blackness from baked on fluxes and no longer wets properly, information technology is time for the cleaning tools of last resort. Tip tinner (Plato #TT-95) is a combination of lead-gratuitous solder and cleaner. While the soldering iron is at total temperature, scroll it in the tip tinner. Equally you curl information technology, it should alter from blackness to shiny silver as the baked flux is cleaned off. Then wipe off the excess tip tinner from the soldering tip, and re-can using wire solder. Don't let the proper name fool you – "tip tinner" is not intended to exist left on the tip.
Polishing bars are also available and are used to scrub the tip make clean of flux residues. This should but be used as a concluding resort considering y'all will be removing iron along with the burnt flux. Once a tip shows pitting - bodily holes in the iron - it is time to be replaced.
Associated products:
- Plato Sponges
- Plato Brass Tip Cleaner
- Plato Tip Tinner
Is a brass "brillo pad" or sponge meliorate for cleaning soldering tips?
Similar everything else, in that location are pros and cons to each:
Brass Tip Cleaner
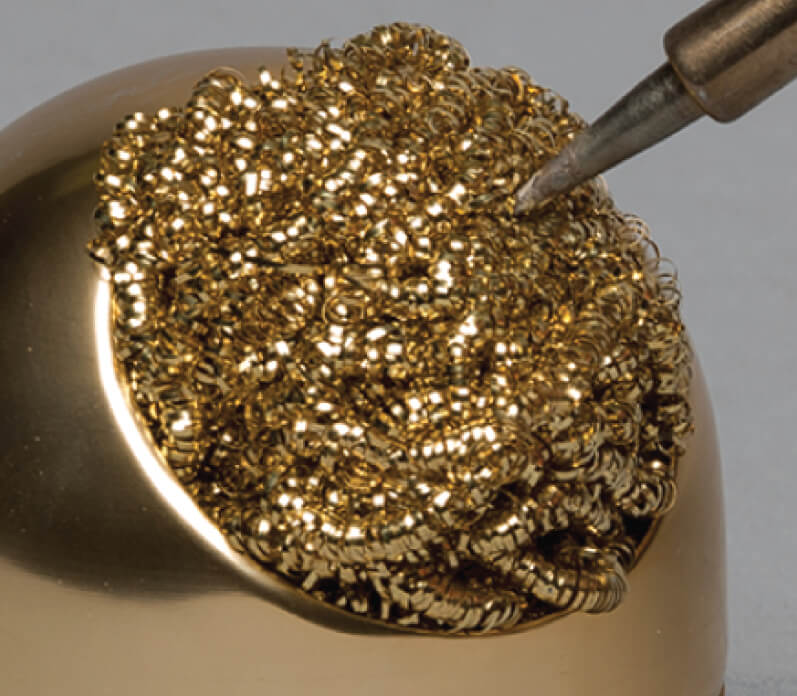
- Pro-Fast and piece of cake to use, doesn't require saturating with water, and doesn't thermally shock the soldering tip.
- Con – It is abrasive, fifty-fifty though brass is softer than the fe on the cease of the tip. It has more of a tendency to scratch the chrome plating, which keeps the solder from wetting up the tip. That could allow corrosion to creep in nether the plating, reducing the lifespan of the tip.
Remember to use a jabbing move using a contumely tip cleaner. Wiping beyond the surface increases the likelihood of flinging molten solder.
Cellulose Sponge
- Pro – It is an effective and fast way to clean a tip. They come with different holes or slits to brand it even faster and easier, and to avoid flinging molten solder.
- Con – Cools down the tip, so requires the tip to estrus upward again. Information technology also can thermally shock the tip, especially if the sponge is overly saturated. This can shorten the tip life by creating micro-fractures in the iron plating.
Make sure yous are using a cellulose sponge that is intended for cleaning soldering tips. Cellulose is a natural fabric derived from wood lurid. It will not cook and damage the soldering tip as a constructed sponge would. The sponge should not be soaking wet, just lightly damp. Wring it out thoroughly later saturating with Deionized (DI) water. DI water is recommended to prevent mineral build-upwards on the soldering tip. Once your soldering tip has been cleaned, remember to re-tin by melting on a minor amount of solder on the end of the tip. This prevents the working terminate of the tip, which is atomic number 26, from corroding when exposed to air over a menstruum of time. Associated products:
- Plato Sponges
- Plato Brass Tip Cleaner
Should I clean all the solder off the soldering tip later on I'm finished soldering?
It is a common practise to wipe down the soldering tip before putting it back into its holder. This exposes the raw atomic number 26 on the working terminate of the tip, which volition rust in the open air. Add together whatsoever residual flux to the mix, and y'all take a prematurely pitted soldering tip. Before taking a intermission or stopping for the day, wipe off rest flux and solder, and re-can by applying fresh solder to the finish of the tip.
What can I do to increase soldering tip life?
Since the motion from lead to atomic number 82-gratuitous solders, a common complaint has been short tip life. The higher heat needed for lead-free solders and flux combined with greater activity leads to faster tip burn-out. Often the tips plough blackness, the solder beads and just drips off the finish of the tip. It may likewise be referred to as a "cold tip", just have intendance not to touch it with your bare fingers!
Soldering tips have a copper core that transfers heat from the heating chemical element to the working end (tip of the tip). Because copper is very soft and easily corroded and worn abroad, other metals are used to plate over the copper, including an outer layer of iron. Although fe is very difficult, it will nevertheless corrode somewhen. In addition, it can be coated with flux and other soils, which can crusade dewetting. Corrosion and dewetting will slow down soldering and eventually necessitate scrapping the tip. Although all tips volition accept their solar day in the trash bin, there are several steps an operator can take to increment tip life:
- Reject the heat
- Properly clean the tip
- Can the soldering tip
- Utilize special cleaning tools
When leaving the solder station for anything over 5 minutes, turn it off. When yous exit the station turned on, the tip remains at soldering temperature, further reducing tip life. Modern soldering equipment heats up to a soldering temperature in seconds, so the time savings is not worth the reduction in tip life.
Associated products:
- Plato Sponges
- Plato Contumely Tip Cleaner
- Plato Tip Tinner
When should I throw away an old soldering tip?
When the tip is blackness and dewetting (solder doesn't cling to it), called a "cold tip", it can generally be cleaned and used over again. Once there is pitting and visible corrosion, it is fourth dimension for a new tip. The outside of a soldering tip is plated with iron over the thermally conductive copper center. This protects the soft, corrosion-prone copper from the harsh fluxes. Once flux gets through the iron plating through pits, the tip will be eaten away quickly.
How can I avert corrosion on the PCB subsequently I'grand finished soldering?
Flux residues can cause dendritic growth and corrosion on PCB assemblies, and so make sure y'all're using best practices and cleaning the board. After all, the components have been replaced and excess solder removed…
- Clean the area thoroughly with a quality flux remover.
- Bending the board to allow the cleaner and residues to run off.
- If needed, utilise a horsehair castor or lint-costless wipe to gently scrub the PCB, and and then follow with a rinse.
- If using a wipe, make certain it doesn't exit fibers/lint on your PCB, which may cause bug later.
This is an optional step for no-clean flux, but still a adept idea for densely populated or high voltage boards. It is admittedly required, regardless of the flux blazon, if you lot program to follow your repair with conformal blanket.
Associated products:
- Techspray G3 Flux Remover
- Techspray E-LINE Flux Remover
- Techspray Brushes
- Techspray Wipes
10 tips to good soldering
- Start with a clean surface.
- Friction match the size of your wire solder to what you are soldering.
- Lucifer your soldering tip to what y'all are soldering.
- Select your solder and flux carefully.
- Keep your tip clean and tinned.
- Select a soldering temperature that is hot enough to efficiently melt the solder, but non too hot.
- Agree the soldering tip to the lead and contact point/pad until both are brought up to temperature.
- Employ plenty solder to cover the contact pad and surroundings the lead.
- If necessary, trim your leads with a sharp shear lead cutter, and don't trim into the solder articulation.
- Clean flux residues from the soldering expanse with a quality flux remover.
Associated products:
- Plato soldering tips
- Plato shear lead cutters
- Techspray G3 Flux Remover
- Techspray E-LINE Flux Remover
That concludes our Ultimate Guide to Electronic Soldering. Still accept questions about which soldering products are all-time for your applications? Contact united states at 678-819-1408, or send united states a bulletin here.
Source: https://www.techspray.com/ultimate-guide-to-electronic-soldering
0 Response to "what you need to do small wire soldering"
Post a Comment