How to Clear Obd2 Codes Without a Scanner
Having your own scan tool right there in the glove box is just as important as a set of booster cables in the trunk. Code readers get you to the business end of the problem real fast. But they don't always work, I've been a mechanic for over twenty years and here I'll share common reasons codes won't clear.
The top 4 reasons a scan tool won't clear codes:
- Fault codes are live faults
- Incorrect code clear procedure
- Scan tool faults
- Scan tool won't communicate
There are a few reasons why fault codes won't clear and I've listed them in order of how common those reasons are. In this post, you'll learn how to diagnose why your scan tool won't clear your vehicle's fault codes and what you can do to fix it.
1 Fault Codes Are Live Faults
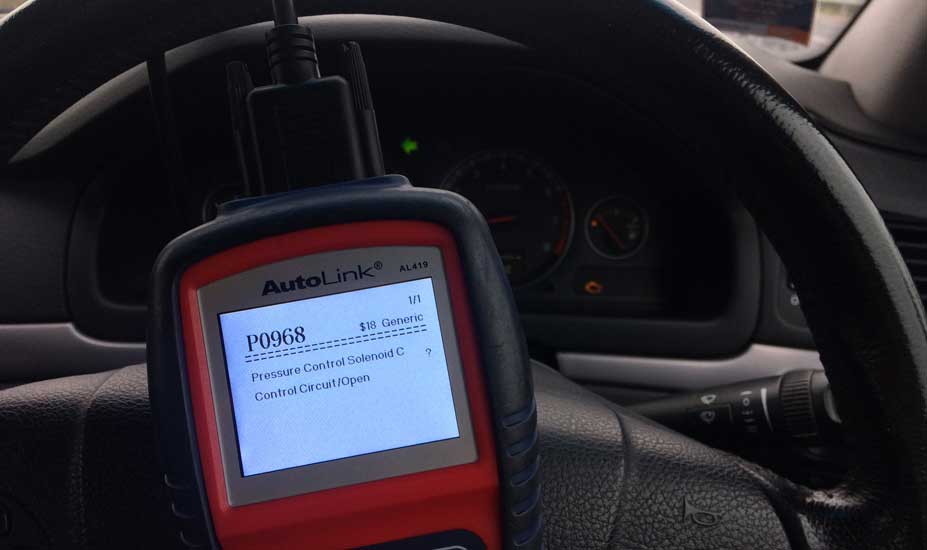
Your fault codes are live, this is the most common reason why your vehicle's fault codes won't clear. I'm assuming all is good with your scan tool, it powers up when you connect to the OBD port (if it doesn't see "Scan tool faults below").
Most scan tools automatically communicate with the vehicle modules over the communication network. I'll also assume your tool communicates with the vehicle modules and doesn't respond with "No Communication" if it does see "Scan tool faults below".
Code readers are also known as scanners read hard and soft codes. Technicians describe Hard codes as live current faults, that's a fault that comes back just as soon as you clear it.
A technician may describe soft codes as historic anomalies or intermittent codes that don't affect vehicle function.
Hard codes on the other hand are current static faults that are affecting vehicle system performance. These types of codes need to be repaired before they can be cleared from the computer module.
After diagnosing and repairing the fault codes successfully, clearing the codes may require following a set procedure, see "Incorrect code clearing procedure" below.
2 Incorrect Code Clear Procedure
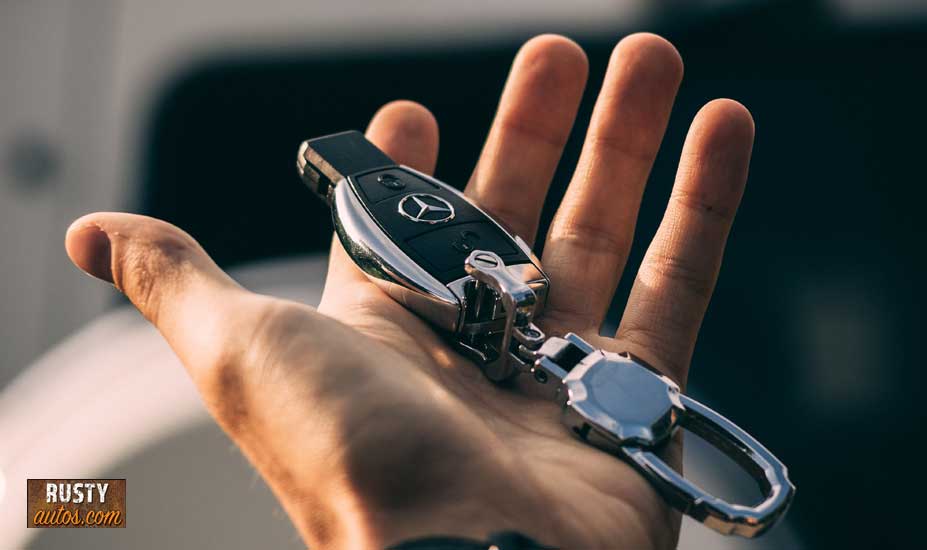
Clearing codes can normally be achieved by simply hitting clear codes on the scanner and job done. However, some vehicles or modules may be a tad more sensitive to procedure.
It is not unusual for computer modules to experience a brain fart (logic lock) and just need time to get their crap together.
Try this procedure when codes are stubborn and won't clear after a repair.
- Ignition On
- Clear code
- Ignition Off
- Key out and lock vehicle
In addition, try also:
- Ignition On
- Clear code
- Ignition Off
- Wait one minute
- Drive vehicle through drive cycle
Bear in mind some components require calibration or flash coding after replacement. These may set fault codes that won't clear until the system resets or is flash-coded.
Similarly, replacing modules with used modules from other cars generally won't work, control modules are coded to the original car's chassis number.
Replacing or disconnecting a car battery for example will often require recalibration of steering angle sensors and throttle body position sensors etc. A few days of driving usually helps reset these components but issues can arise.
3 Scan Tool Faults
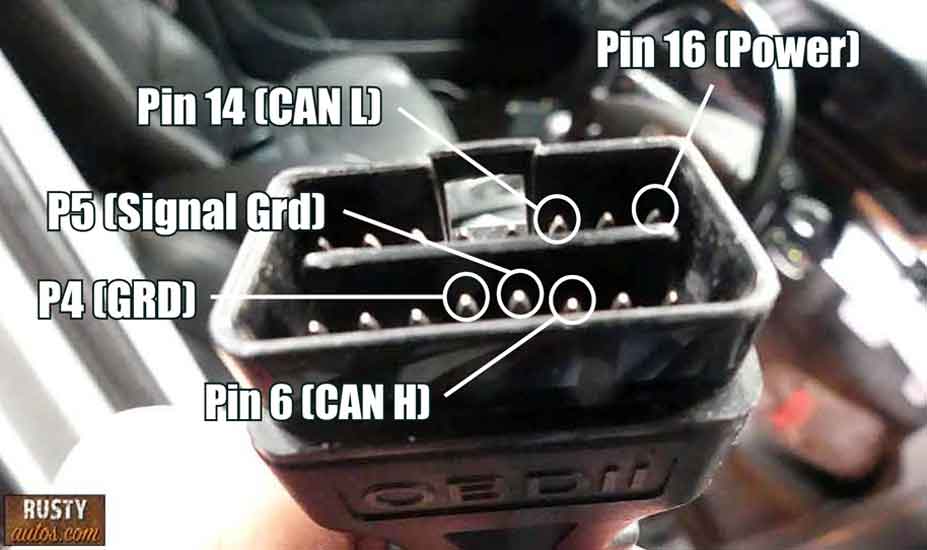
Scan tool faults aren't that common, I've never broken a tool yet but I have worn out a few cable connectors. Here's a list of scan tool problems and what you can do to fix them:
- No power in the scan tool – The most common cause of no power in the tool is a blown OBD vehicle fuse. If the check engine light doesn't light up on ignition the fuse is blown. It commonly blows because it shares a fuse with the vehicle's 12 volt power point or the cigarette lighter. Check the fuse box for 12 volt, cig lighter and OBD listing.
- Scan tool plug connector fault – I've worn out a few of these guys, they work hard and wear out. The tools plug spades can become bent or worn which causes a poor connection or no connection. Wiggling the plug in the OBD port usually lets you know it's time to change the cable.
- Check the OBD port – The data link connector (DLC) terminals may be damaged. Years of wear or worse, front probing can spread the contacts causing poor or no contact with the scan tool. Check the wiring behind the connector too.
- Blown scan tool fuse – Your scan tool is fused, if it's easy to access the fuse, check it out. If not, take your scan tool to another car and verify it works.
- Tool software – Make sure your scan tool has the latest and greatest software installed. Many tools offer free updates.
4 Scan Tool Won't Communicate
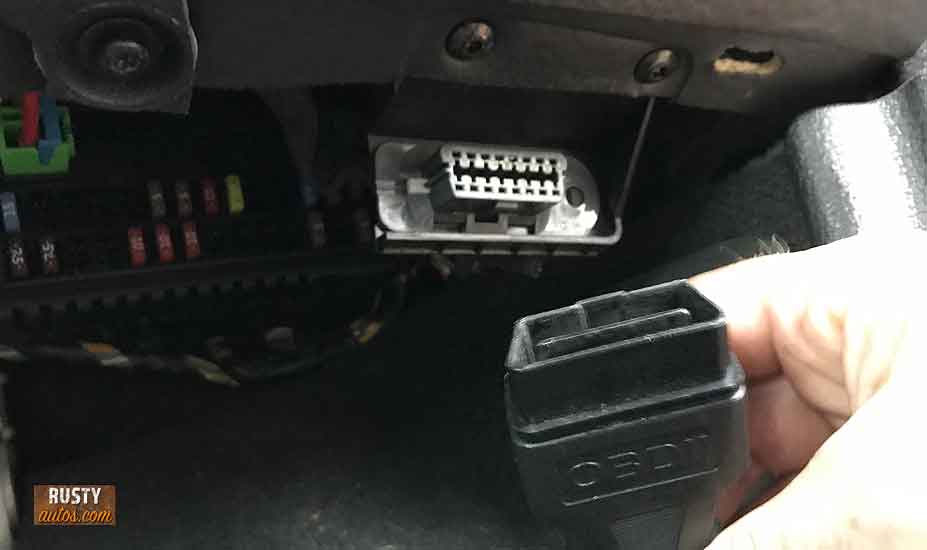
If your scan tool throws back a dreaded no communication code (U – xxxx), we'll need to roll our sleeves, we'll need a good DVOM and a wiring diagram to start with. A scoping tool works best for capturing glitches in network systems. But we'll work with just a DVOM as most will have access to a voltmeter.
While total communication loss is rare, it's more usual for one module to go down, and the other working modules report its loss by setting a fault code.
A scan tool commonly won't communicate because one faulty module is pulling the whole system down. A damaged circuit is common too, but not as common as a failed module.
We need to isolate the fault, identify it and replace the module or repair the wiring, etc.
Your vehicle is stuffed with modules, each one tasked with a particular system to manage. Your ECU (Engine Control Unit) takes care of the engine, your TCM (Transmission Control Module) takes care of the tranny, BCM (Body Control Module) takes care of the vehicle accessories. You get the idea.
See the scan tools I recommend here on the "Mechanics tools page".
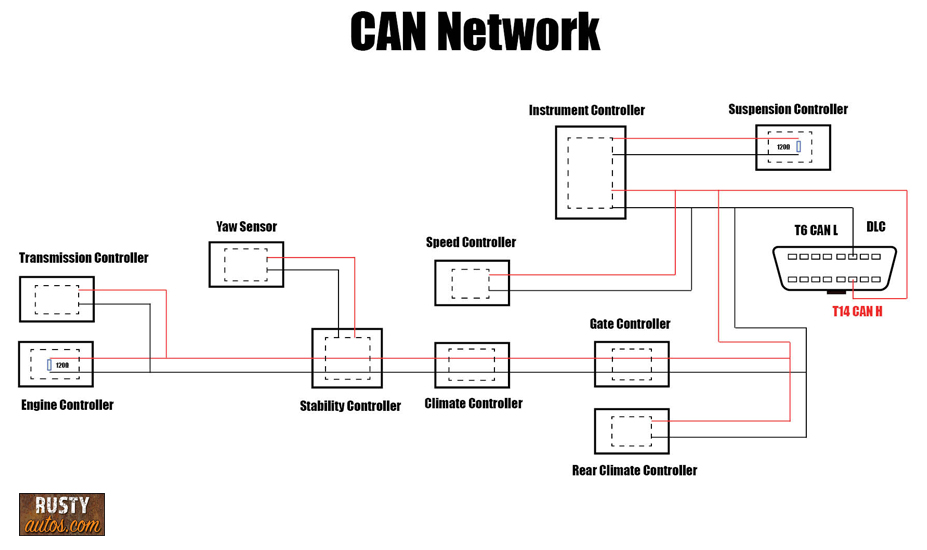
All these modules (aka nodes) communicate with each other using a system known as CAN (Controller Area Network).
CAN employ a twisted pair of wires (one wire CAN high 3.5-2.5 volts oscillating and the other, CAN low 2.5 – 1.5 volts oscillating) that loop the vehicle connecting all the modules on the network.
Experience has shown me it's best to look for clues and ask some questions if needed before testing components. I'll look for signs of recent accident damage, water leaks, heavy corrosion, or recent works carried out on the vehicle.
Looking at a vehicle and asking a few questions may point you in a direction that can save you a ton of time and hard work. Assuming I find nothing suspicious or interesting on an initial look over, I'll make a few basic checks.
A good power supply is super important to modern vehicles and so I like to verify that there's stable power and ground supply.
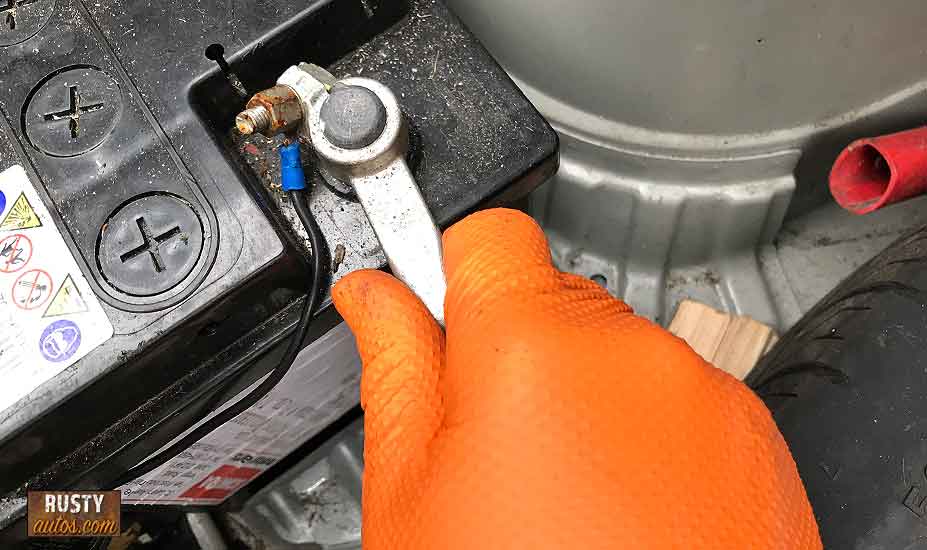
I'll check the following:
- Battery voltage
- Check battery terminals clean and tight
- Test battery
- Chassis ground
- Check engine ground
Now I'll move on to check for signs of life in the DLC. I'll check power, ground, and communication network voltage. I'll use a DVOM set to volts DC for these tests.
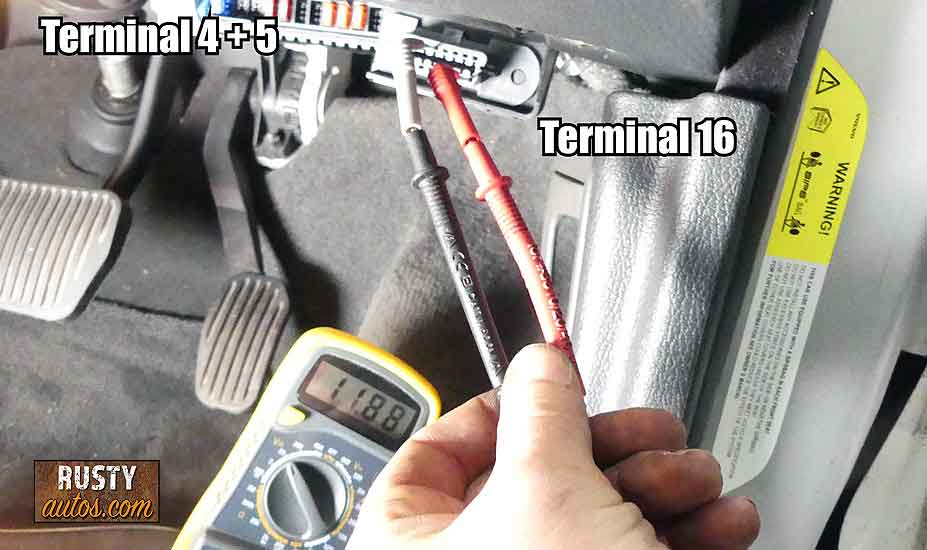
- Check power at the DTC (Terminal 16) – Above 12.5 volts ok
- Check ground (Terminal 4) – Reverse a test light or use a voltmeter
- Check chassis ground (Terminal 5) – Reverse a test light or use a voltmeter
- Check CAN high voltage at (Terminal 6) – Normal 3.5 to 2.5 volts (voltmeter set to peak min-max capture)
- Check CAN low voltage at (Terminal 14) – Normal 2.5 to 1.5 volts (voltmeter set to peak min-max capture)
Now we'll need to check for resistance on the CAN network and for this test, we'll use our DVOM set to read ohms. This test is performed when the network is asleep, removing the battery negative lead works best. Back probing at the DTC as it won't spread the pins, or use a fine tool like a test probe.
- Check resistance between CAN high (Terminal 6) and Can low (Terminal 14) – A reading between 55 and 65 ohms is acceptable. Any reading outside this suggests a problem on the network.
This test won't work for all vehicles, it will depend on how the vehicle's communication system is configured. Some systems may use a gateway module that limits the usefulness of probing the DLC. In such a vehicle a reading at a module harness is more valuable.
It's often more useful to find an accessible module that uses the same network (some vehicles have more than one network) like an ABS module or electric steering module.
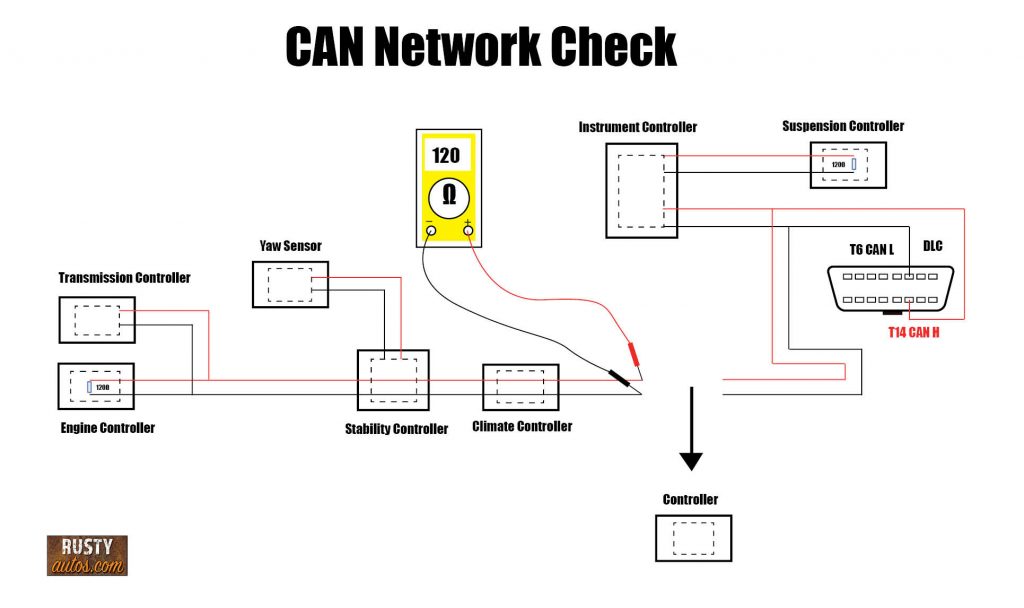
For a more detailed post on CAN network repairs check out OBD won't connect to ECU
The test goes like this:
- Power down the vehicle by removing the battery.
- Remove the module connector.
- Identify the two sets of twisted pairs (CAN high and low) in and out of the module. (This divides the network into two halves)
- Check resistance on the pair in.
- Check resistance on the pair out.
- A reading as before of about 120 ohms is normal for each of the circuits
- The pair with abnormal reading is the side of the circuit with the problem. (you can split that circuit in half again by referencing a diagram and repeating the test and so on until you isolate the fault)
- If by chance your readings for both twisted pairs are normal, it suggests a possible issue with the module unplugged. (you got lucky)
It is possible to identify the failed unit by a process of elimination, however a wiring diagram and approaching it in a systematic manner is faster and a ton less work.
Need to buy an inexpensive scanner that gets the job done, check out the Topdon vs Autel code reader review or, check out the scanners I recommend here on the "Mechanics tools page".
You can find the wiring diagram and all the tools I use to fault find these types of problems here on the Auto electrical repair tools page.
How to Clear Obd2 Codes Without a Scanner
Source: https://rustyautos.com/obd-ii-wont-clear-codes/
0 Response to "How to Clear Obd2 Codes Without a Scanner"
Post a Comment